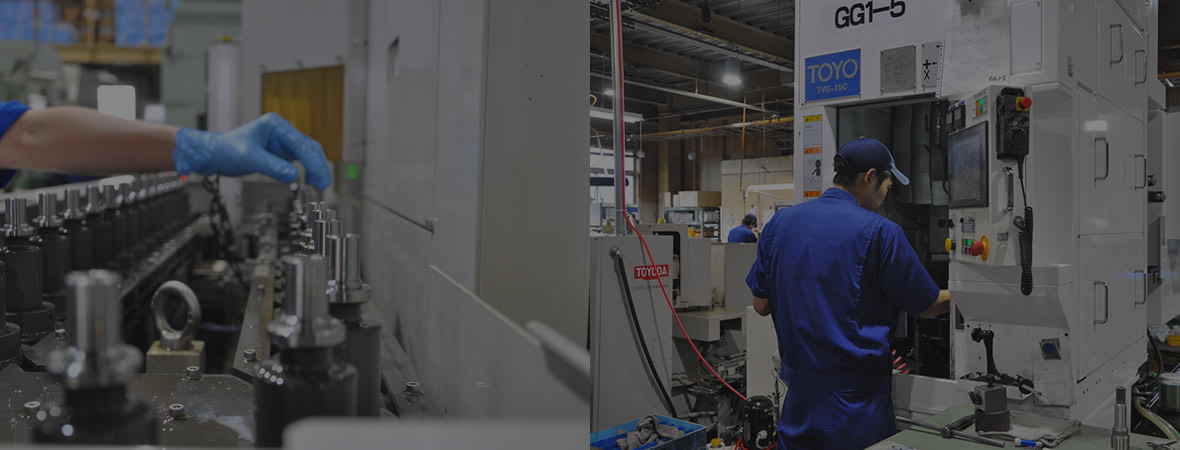
-
Flow 01,Process drawing.
Based on customer product drawing, create the processing drawing.
-
Flow 02,Material procurement.
Based on customer material specification, arrange the material.
such asSCM415, SCM435, S45C, AL etc.
-
Flow 03,Gear blank process (Lathe cutting)
This process is the base of accurate gear manufacturing.
-
Flow 04,Broach, Slotter process
Based on required shape ( spline, serration, keyway etc.)
will be made by special purpose machine. -
Flow 05,Gear Cutting
Remove burr, kaeri when cutting.
Using high accuracy Hobbing M/C or Gear Shaping M/C.
(Old) JIS 1st class also possible to manufacture as per request. -
Flow 06,Chamfering and de-burring
Chamfering, de-burring process
-
Flow 07,Hardening (Heat treatment, Surface treatment)
Based on material, Heat treatment or surface treatment will be done. This treatment is hardening the gear.
(Carburizing, Induction hardening, Ion nitriding hardening etc) -
Flow 08,Grinding (Inner diameter, Outer diameter, plane surface)
Grind the distorted area where created by hardening process, Then meet the required size and surface roughness. This is hard turning process and using ID, OD, Plane grinding M/C or Lathe M/C.
-
Flow 09,Gear grinding or Skyving
This process is to grind the gear tooth.
Using grinding stone or ultra-hard hobb cuter.
This process makes higher accuracy gear. -
Flow 10,Inspection
Based on customers requirement, experienced inspector will be checking the product by using the latest testing M/C.